
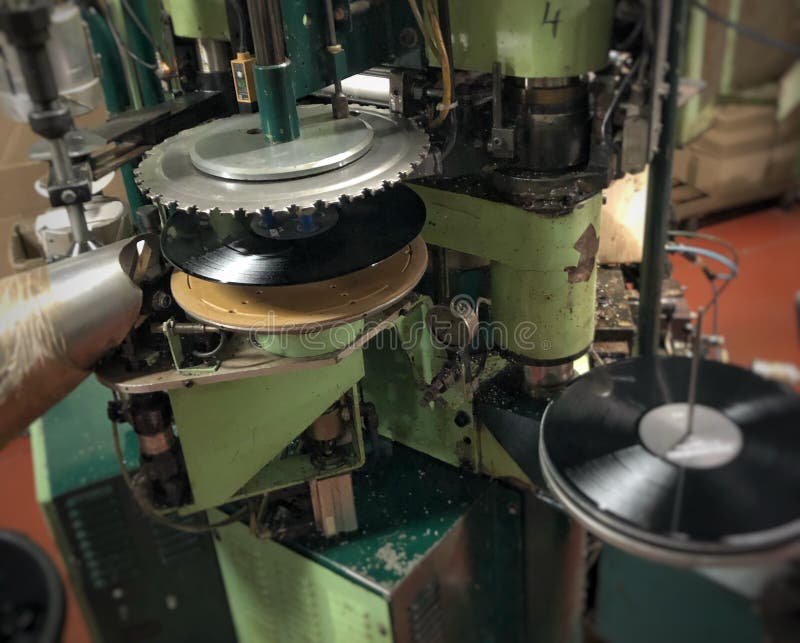
This ensures that cutting grooves in the record do not crash into each other, and that disc space is maximised in quiet passages. This piece of equipment listens to the audio signal and pushes the head across the lacquer at a higher or lower rate depending on the audio level. The cutting head is pushed across the rotating lacquer by the ‘vari-groove’.

The master lacquer is rotating at the specified playback speed, and the cutting head is lowered onto it. These two ‘drive rods’ meet at the cutting stylus, which can be driven in both the horizontal (level) and vertical (stereo) axis. The cutting head is two very accurate, small, loud speakers with magnets which drive 2 metal rods (1 per channel). This amplifies the audio from the line level input and sends the signal to the ‘cutting head’. These are high quality audio amplifiers, around 600watts per channel (left and right). Here the signal is first passed through the RIAA curve system and then into 2 power amplifiers. This is achieved by sending the mastered audio to the cutting amp rack. This is an acetate coated aluminium disc, 14” diameter. Once a good mastered sound is achieved the audio is cut onto a master lacquer. If there are one or two loud crash cymbals or sibilant vocals, these can be reduced with careful set-up, so as to not reduce the specific frequency for the whole track. Multiband (the signal split into treble/ mid/ bass) compressors/ limiters can also be used. This means a louder sounding signal can be cut. The levels are controlled by reducing the impact of peaks/transients in the audio.
Vinyl record pressing series#
The mastering involves playing the audio through a series of EQ’s (where treble, mid-range and bass content can be altered) and compressor/ limiters. Once the audio is complete and saved as a file (wav/aiff) it will be sent to our vinyl cutting suite where it will be mastered. Generally one stamper is good for around 1,000 records, before it splits in the press or is worn out / discoloured.Īfter separation, the stamper is trimmed and ‘formed’, ready to be fixed into the press. Several of these can be made from the positive. The same process is applied to make the ‘stampers’. This is the positive, which is an exact playable copy of the master lacquer.Īfter separation from the negative, the positive goes into the plating baths. This negative is cleaned and coated with a ‘passivator’ and then goes back into the plating baths to make a ‘positive’ by the same electro-plating process. This is called a ‘negative’, as it is a mirror image of the lacquer. After this process, enough nickel has been plated on the disc to support itself. This deposits nickel onto the silvered disc and goes on for one and a half hours. This process involves the silvered disc being submerged in a nickel solution and connected to the electric terminals for the plating procedure. This penetrates the lacquers’ grooves with exact accuracy and prepares it with a metal surface ready for the electro-plating process. ‘Silvering’ is where the lacquer is placed on a slowly rotating vertical turntable and sprayed with a very fine silver nitrate spray. The lacquer is then ‘sensitised’ in a liquid ‘dip’ preparing the lacquer for ‘silvering’. Once the master lacquer has been cut it is ‘processed’ into metal ‘stampers’ that are used on the pressing machines.įirstly, the lacquer is cleaned carefully using a washing system where no human contact is made other than with liquids.
